What it does:
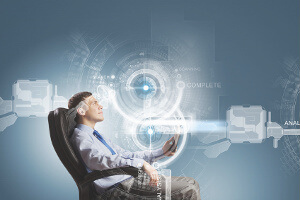
The Aboard Active Supply Chain Optimizer (ASCO) permanently keeps all the merchandise requirements procured at the company using the ERP suite. It applies to
companies doing manufacturing (both discrete and process) and distribution of any type (importers, exporters, wholesalers, etc.).
Requirements come from actual sales orders, from forecasts of sales and from merchandise items going below their minimum inventory levels.
The ASCO constantly procures merchandise required, by creating production work orders and purchase orders, so merchandise will be permanently kept at or above
the minimum inventory levels and customer orders will always be shipped when scheduled.
Other optimizing ERP/MRP systems provide users with the information and tools to achieve the same goal of optimizing the supply chain, but do this through a
periodic batch update initiated by human users. ASCO does it differently in that it takes the initiative and proactively instantly creates and schedules
production work orders and purchase orders as needed.
Production work orders are created down the production tree, through unlimited levels of bills of materials, to manufacture work in process items or subassemblies
as needed, until at the leaves of the branches of that production tree purchase orders are placed when raw materials or basic components are insufficient for the
entire manufacturing tree to be put in production.
We call that "active" behavior, because the system procures merchandise instantly, for example, when the Save button is clicked for a new sales order that
contains line items that are on back order because there is not enough inventory to fully commit to the order the merchandise sold.
The production forest of many individual production trees is permanently kept updated, and when changes are introduced, because a new sales order is input, or
when existing merchandise is shipped and the items go below their minimum inventory levels, or when sales forecasts are changed, the system indefatigably revises
the production and purchase schedules to make sure that everything is properly procured to arrive just in time.
How it does it:
The ASCO adds a virtual robotic user to the traditional ERP.
You can think of the Active ERP (aERP) as two parts, a traditional ERP plus a "virtual user", a robotic user implemented by the ASCO software, that uses the
traditional ERP system to create activity to run your business optimally.
The active robotic virtual user is the indefatigable production manager and also the indefatigable purchasing manager that are permanently looking for things
that the company needs to manufacture or needs to purchase, and when some new merchandise requirement is added, the robotic virtual user instantly procures for
it, going down the production tree to create additional production work orders for work in process items needed and purchase orders for materials and components
needed.
There is a third very important component that you could add to this two-part system, which is an interface with the human users that allows them to monitor,
review and eventually supersede the decisions of the robotic user to accommodate local and/or temporary situations for the manufacturing and purchasing.
The system always alerts the human users when an order cannot be shipped on time for any reason, prompting for sales team to call the customer to reschedule the
delivery date which was identified as impossible to meet.
When situations change because the deliveries from vendors are delayed or any other reason, the system adjusts the optimal schedule and notifies the human users
when the changes result in not being able to meet scheduled customer deliveries, again prompting the sales team to contact the customer to notify a new shipment
date.
The optimizer is always looking for changes in the production plan, maybe made by human users to adjust for real life situation such as a machine needing repair
and always keeps the schedule optimized but respecting those changes made by the human user.
The new work order and purchase order schedules are based on current open purchase and work orders, purchasing and manufacturing lead times and preferences for
minimum quantities to be ordered from vendors or manufactured in the plant. Schedules can always be revised by the human users, even for past days, so if a
scheduled activity could not be completed yesterday due to any incidents at the plant, for example, the human users can adjust production work order dates as
needed, and they will be told when an adjustment is critical and would delay a shipment commitment. The system provides a graphical depiction of the dependencies
of shipments on production work orders at any number of levels deep and ultimately on purchase orders of basic components and raw materials.
Production work orders are declared "Released" when the production manager considers them complete, having gone through their entire manufacturing process and
having successfully cleared the Quality Control tests and having been approved by the Quality Control Lab.
Similarly, the purchasing manager sends to the vendors the Purchase Orders scheduled by the system, and later, when the merchandise arrives, supervises the
process of reviewing the merchandise purchased.